what is ferrochrome processing
The largest user of chrome ore is the ferroalloy industry. It accounts for about 80% of the total output of chrome ore. The chromite ore used for smelting ferrochrome is generally required to contain 340 to 50% of Cr2O. The ratio of chromium to iron is greater than 2.8.
Ferrochromium alloys are classified into high carbon ferrochrome, medium carbon ferro chrome, low carbon ferrochrome, and micro carbon ferrochrome according to the difference in carbon content.
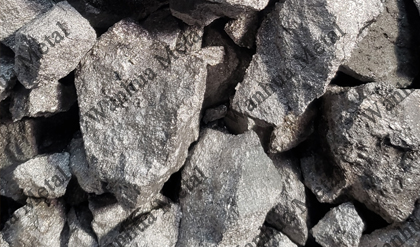
High Carbon Ferrochrome
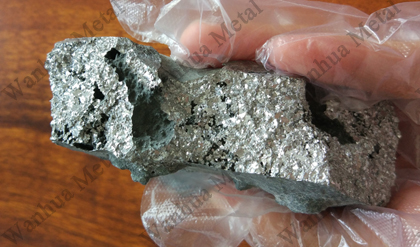
Low Carbon Ferrochrome
Medium, low and micro-carbon ferrochrome alloy are generally made of silicon-chromium alloy, chromite and lime. Desiliconization is refined with a 1500-6000 kV electric furnace. It is operated with a high alkalinity slag (CaO/SiO2 is 1.6 to 1.8).
Low-carbon, micro-carbon ferro chrominum is also produced on a large scale by the heat exchange method. Two electric furnaces are used in production. A furnace smelts silicon-chromium alloy, and a furnace melts slag composed of chrome ore and lime.
The refining reaction takes place in two phases:
1. After the slag of the slag furnace is injected into the first barrel, the silicon-chromium alloy which has been initially desiliconized in the other barrel is exchanged. Since the excess amount of slag oxidant is large, desiliconization is sufficient. Therefore, micro-carbon ferrochrome containing less than 0.8% silicon and as low as 0.02% carbon can be obtained.
2. The slag (about 15% containing Cr2O3) in the first barrel is moved to the second barrel. Then, a silicon-chromium alloy (silicon-containing 45%) which is silicon-chromium electric furnace is heat-exchanged into the slag. After the reaction, a preliminary desiliconized silicon chromium alloy (about 25% silicon) was obtained. Further desiliconization is carried out in the first barrel, and the slag containing Cr2O3 is less than 2 to 3% and can be discarded.
Oxygen blowing to refine low carbon chrome iron
Refining of ferrochrome low carbon.Liquid carbon ferrochrome is used as a raw material. During the blowing, a small amount of lime and fluorite are added to the molten pool to form a slag, and a silicon-chromium alloy or ferrosilicon is added before the iron is discharged to recover the chromium in the slag.
Refining micro-carbon ferrochrome by vacuum solid state decarburization
The blowing of micro-carbon ferrochrome is only possible under a certain degree of vacuum. Use finely ground ferrochrome high carbon as raw material. A part of the ground high-carbon ferrochrome is oxidized and calcined as an oxidizing agent, and is added with water glass or other binder to form agglomerates.
After being dried at a low temperature, it is heated and reduced in a vacuum of 0.5 to 10 mmHg at a temperature of 1300 to 1400 ° C for 35 to 50 hours in a vacuum furnace. Micro carbon ferrochrome containing less than 0.03% or even less than 0.01% carbon can be obtained.
Chromium is one of the important strategic materials. Due to its hardness, wear resistance, high temperature resistance and corrosion resistance, it has been widely used in the metallurgical industry, refractory materials and chemical industry. Anyang Wanhua Metal has been committed to the production of ferroalloys for many years. In recent years, it has performed well in high and low carbon chromium iron.